MC1332/H外圆磨床数控化改造方案和实现
发布日期:2016-03-04 来源:作者:孙丽萍 邹轩 上海理工大学
点击数:38969
一、经济型数控化改造实施方案的可行性
普通外圆磨床MC1332/H主要适宜磨削IT6到IT5精度的圆柱形或圆锥形的回转体工件,在军工、航天、汽车等行业有着广泛的应用。近些年随着国内装备制造业的快速发展,带动了机床改造市场,国内一些企业开始使用经济型数控系统改造普通磨床,效果显著。
首先,改造后的数控磨床MC1332/H比普通磨床有优越性,体现在:它能够解决机械制造中结构复杂、精度高、批量小、零件多变等加工问题;并且能稳定产品的加工质量,降低劳动强度;由于数控系统有很强的运算、记忆和存储能力,可存储多个加工程序;它还具有自动报警、自动补偿等功能,能提高自动化程度,给操作人员提供便利。在实际的生产过程中,一名操作人员可看管多台机床,这不仅节省了劳动力,还大幅提高生产效率,降低了人工成本。其次,随着国产经济型数控系统技术的不断发展,它的稳定性也在不断提高。所以,国产经济型数控系统不仅能满足实际加工需求,而且价格是同类型进口系统的1/5,明显体现出经济型的特点,能大大降低设备的改造成本。此外,采用原来已经成熟的机械结构本体,能实现机床的大批量改造,缩短新设备试制周期和生产周期,进而快速响应市场变化,扩大产品市场占有率。
综合以上分析,普通外圆磨床MC1332/H经济型数控化改造实施的可行性很高,改造后不仅能满足生产功能要求,提高自动化程度,而且能大大提高磨床的加工精度,扩大加工范围,使企业充分利用有限资源,降低制造成本。
二、MC1332 /H改造遵循的三原则
1、“少更改”原则
经济型数控化改造的基本原则是在满足需要的前提下,应尽可能减小改动量,最大限度地利用原有设备的硬件资源,以降低成本。“少更改”原则的前提是要提高磨床制造质量,从控制线路改进的源头着手,增加使用的可靠性和耐久性,减少返修率和退货率,从而延长其技术寿命周期。先根据上述“少更改”的原则,以改造后磨床要达到的各种精度、驱动电机的功率和用户的要求为基准,只把与数控系统有关的部分进行重新设计,可最大限度地减少成本,节省设计制造时间,减少废弃物产生,提高资源再次利用率。
2、简化和低消耗原则
改造时应尽量简化设计,使用多功能部件及模块化的部件来简化产品结构,当发生故障时方便用户检查和维修。一方面,在满足生产工艺控制要求的前提下,简化控制回路的逻辑设计,可节省元器件,方便操作;另一方面,所用到的电气元器件数量愈少,工作过程中出现故障的概率就愈小,稳定性就会愈高。此外,在设计过程中要做到:合理使用和分布电气件和线路,使用抗干扰能力强的电气元件,尽可能远离干扰源与干扰对象,高压线路、脉冲引线、低电压线路分别敷线,输入端口和输出端口分开等。
3、可扩展、升级原则
改造时不仅需要考虑系统本身的寿命,而且要考虑产品功能的更新。首先,通过更换功能模块,实现产品较为简易且廉价的升级。对于磨床用户当前不要求的功能,在设计时可将这些功能作为推荐可选部件,留下相应的设计空间,方便用户生产过程中的功能添加。其次,采用可进行实时软硬件升级的数控系统,用户可对数控系统进行更新、程序更改及资料备份,避免用户重新购入设备造成的资源浪费,这既可以延长设备的使用周期,也可以提高设备利用率。
三、MC 1332/H改造过程
MC1332/H的改造基于以上3条基本改造原则,一般从3个部分:机械部分、液压部分、电气部分进行改造。由于MC1332/H机床机械部分各方面性能稳定,精度高,液压系统工作正常,所以改造时基本采用原有的机械及液压零部件。下面重点阐述电气控制部分的改造过程。
1、电气控制部分方案
普通外圆磨床MC1332/H的电气控制回路是由继电器来实现控制的,虽然实现的动作并不多,但是控制较复杂,且安全互锁较多,因此电箱中的电路显得十分复杂。MC1332/H砂轮架进给运动是通过人工手摇实现的,工作台面的左右运动是由液压驱动换向阀实现的。这种方式精度不高,也不能完成成型砂轮修整任务,所以用途局限。
采用经济实用的数控KT630系统进行电气控制部分改造后,在原机床机械基础上,机床两轴(X轴、Z轴)的进给运动分别由数控交流伺服电机通过滚珠丝杠传动; X轴和Z轴上分别设有硬限位和参考点组合开关,极大地简化了外部控制电路。该数控系统实现的是半闭环控制,在满足工艺要求的基础上,虽然它的精度比闭环系统的低,但能满足加工精度的要求。用户能根据加工要求,实现手动和自动磨削控制、砂轮的手动和自动修整、修整后自动补偿等过程,并可对系统数据设定多级密码进行保护;实现机械反向间隙、丝杠螺距误差补偿、系统参数、程序文件的内外存储等。数控系统控制回路如图1所示。
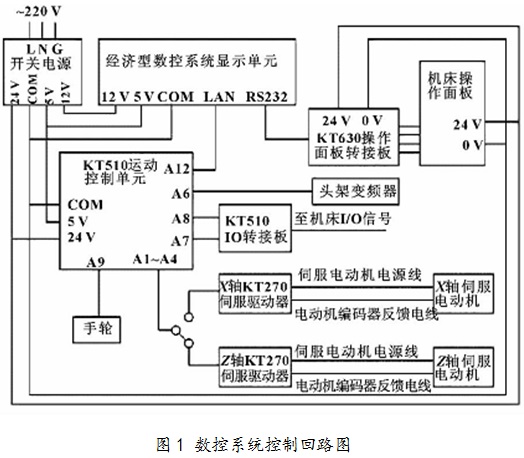
改造后的MC1332/H砂轮架(X轴)伺服电机和工作台(Z轴)伺服电机的进给运动分别由全数字交流伺服驱动系统控制,且分别带有内置编码器;在程序运行过程中,电机速度和位置信号反馈到数控系统和伺服驱动端来保证工件尺寸。头架采用国产变频器控制,可实现速度可调;机床可供用户选配端面测量仪和径向自动测量仪装置。利用端面测量仪,可精确定位砂轮磨削工件切入位;采用径向自动测量仪,可自动在线测量保证工件的加工尺寸。
2、砂轮修整的实现
砂轮修整是数控磨床加工过程中非常重要的功能,而数控磨床相比普通磨床最大的优势则主要体现在砂轮可成形修整方面。MC1332/H采用的是以金刚石笔进行砂轮修整的方式,金刚石笔安装在头架上即图2中1号位置处,两坐标X轴和Z轴运动合成实现复杂的成形砂轮修整过程,修整过程完成后修整量会自动补偿。当金刚石笔安装在尾架上即图2中2号位置时,只能修整砂轮的外圆面,加工范围有限。
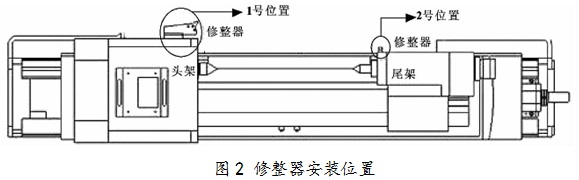
砂轮成形修整是把砂轮修整成与工件轮廓相吻合的形状,使砂轮恢复原有的磨削性能,提高砂轮的磨削效率与磨削表面质量,这一过程的实现是通过X轴和Z轴的直线插补来实现的。修整后的砂轮磨削刃面锐利,磨削效率高,并且砂轮的磨削面形状与加工工件所要求的轮廓形状精确一致,通过一次磨削加工循环,就能完成工件的整个自动加工过程。图3是成形修整后的砂轮与工件匹配的示意图。
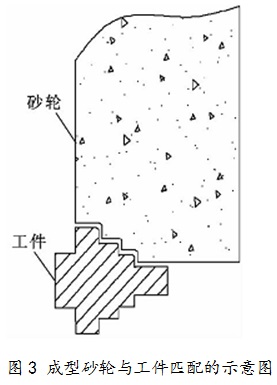
改造前MC1332/H不能进行砂轮修整成型过程,为达到图4所示工件精确的尺寸要求,需进行4次进给加工过程。但因为工件受热变形、砂轮磨损等情况会直接影响磨床的加工精度,在实际加工过程中一次加工工件的挡数不宜过多。受这些条件的制约,限制了加工。而改造后的机床根据工件各挡尺寸要求,将砂轮修整成与工件轮廓相吻合的形状后,可进行一挡成型加工过程,这一过程可节省大约3/4的加工时间,有效地控制生产节拍,扩大了产能。
3、自动加工过程
基于机床的状况和使用特点,采用PLC和NC控制相结合的方法,实现自动循环加工过程。图4是自动循环加工的基本流程,自动或编辑状态下,在模版中更改并保存参数,用户也可直接在电脑中编制和更改模板程序及PLC程序,传输至机床的KT630系统中,当执行自动操作后,机床动作执行由数控系统中程序模板转化来的G代码程序。
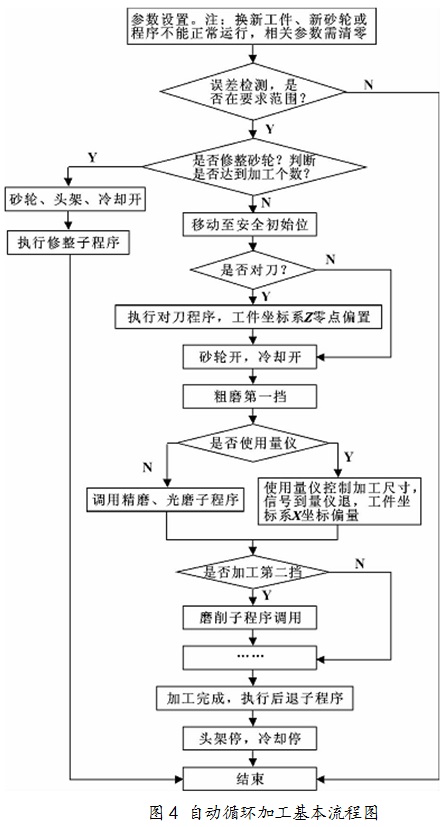
四、辅助功能要求的实现
1、径向自动测量仪(简称量仪)
在实际加工过程中,磨床的加工精度会受许多因素的影响,其中最重要的有以下3种:① 砂轮架体壳的热膨胀。由于砂轮主轴高速旋转,产生热量,导致主轴油发热,引起体壳发热,产生热膨胀。实验表明:砂轮架体壳在开机30min内变化最明显,开机2h后基本稳定,开机4~5h误差最大值能达到0.045mm左右。② 滚珠丝杠引起的热膨胀。由于滚珠丝杠的快速运动,产生热量,引起丝杠膨胀,膨胀值约0.02mm。③ 砂轮的磨损。由于磨削加工过程中会引起砂轮脱落,导致加工出的工件直径变大,这一磨损值受砂轮及工件材料的影响。可以通过冷却油液、更换耐磨砂轮来改善以上因素的影响,但成本太高,而且效果不明显。当工件精度要求高时,比较经济有效的方式是使用量仪来保证加工尺寸。所以为完成一些精度要求高的加工过程,建议用户选配量仪。
量仪的精度直接着影响工件的加工质量。量仪能实现自动在线检测尺寸,其中自定义的M功能中M21、M22分别对应1号和2号量仪的动作开始,M23代表量仪1和量仪2退出。 当测量尺寸到位就立即启动砂轮慢退结束自动磨削,X轴执行删除余程命令,每加工完一挡外圆,系统在X轴后退以前,记下X轴当前的坐标值,从而实现自动预置新的加工零点。
(1)双量仪
如果用户精度要求高,必要时要选用双量仪来保证加工精度。量仪信号点P1、P2(M22、M23指令控制)、P4、P5(M21、M23指令控制)。跳转功能(非模态)是G31,外部P1、P2、P4和P5信号输入后中断直线插补指令的执行,转而执行下个程序段。
(2)同尺寸轴径的多挡在线测量
只用一套自动在线测量仪,通过增加龙门架,利用龙门架上安装的回转油缸带动量仪翻转,可实现同尺寸轴径的多挡在线测量,加工过程中,配随动中心架,采用三点自定心液压动力中心架,驱动油缸与中心架连为一体,可实现∅20~∅60无级变化托持直径,精度高,可满足高速、高精度的要求。
2、端面测量仪(简称对刀仪)
对刀仪是专门用于数控机床的端面定位装置。其核心部件由一个高精度的开关,一个高硬度、高耐磨的硬质合金对刀头和一个信号传输接口器组成。该装置在进入测量工位接触工件的瞬间,触发高电平或低电平信号,机床控制系统接收该信号后发出反馈,完成端面定位。 不论采用哪种对刀方法,其对刀目的是一致的:使机床明确砂轮与工件的相对位置,避免由于工件中心孔有偏差发生撞刀现象,从而保证了加工安全。改造后的机床对刀仪置于砂轮架上,靠工作台运动来确定工件端面位置。在磨批量工件时,由于每个工件中心孔位置有微小的差别,用对刀仪来精确定位砂轮磨削工件切入位;同时确定机床坐标系与工件坐标系的关系。
3、头架准停
在使用对刀仪时,由于工件端面形状不同,会出现对刀不准的现象甚至导致撞刀情况的发生。在加工批量工件时,希望端面测量仪测量同一位置,实现头架准停。MC1332/H的头架电机的运转由交流变频器控制。为了降低机床的制造成本,借助无触点开关来实现自动定点准停,当头架电机停止运行时立即启动头架低速点动,在低速转动的过程中无触点开关信号响应时,电机停转。无论是头架自动运行模式还是手动头架启动模式,这两种情况下自动定点准停都是有效的。
还有一种手动头架准停方式:将无触点开关信号作为头架启动的必要条件信号,工件未摆放到位,就不可执行自动循环程序。显然这需要操作人员转动工件将其摆放到固定的位置,方能自动循环程序。启动这种方式操作量大,但是实现简单,可节省操作时间。
五、结束语
改造后的MC1332/H磨削精度提高,误差减少20%,可靠性好,抗干扰能力强,并且操作方便。我国作为机床制造和使用大国,经济型数控化改造是企业创利增收的一种策略,既能够提高企业的制造能力和制造水平,提升企业的整体竞争能力,提高企业的经济效益和社会效益,也促使国产数控系统在磨床改造领域得到更广泛的运用。