发动机厂数控加工中心维修策略探讨
发布日期:2017-03-14 来源:《上海设备管理》
点击数:35614
目前,数控加工中心在工业领域,尤其是在汽车发动机制造领域受到广泛应用。由于汽车发动机具有加工精度高的特点,且随着近几年汽车在中国市场的逐渐普及,发动机制造逐渐向高精度、高效率、高自动化、高柔性化的方向发展。目前,国内大部分汽车发动机厂的数控加工中心主要以欧美等进口设备的采购为主。虽然国外先进设备的引进为企业带来了活力,提高了加工的节拍和效率,但与此同时,企业在数控加工中心的管理、使用和维护等环节仍存在不少亟待解决的问题,主要表现在设备使用率偏低、故障率高且维修时间和材料成本偏高,从而导致企业的制造和运营成本较高。
一、数控加工中心故障趋势
很多企业在对数控加工中心进行管理和维护时,仍然秉持的是“浴盆曲线”的观点。浴盆曲线是指产品从投入到报废为止的整个寿命周期内,其可靠性的变化呈现一定规律。浴盆曲线的形状呈两头高、中间低,可划分为三个明显阶段:初期故障期、偶发故障期、磨损故障期。
然而,据相关机构统计,现代加工设备符合“浴盆曲线”的概率并不高,以某单位的两种品牌数控加工中心为例,故障率均呈现明显波动(此处故障率是指设备维修时间除以设备计划工作时间。由于加工中心数量较多,此故障率为每月设备平均故障率)。在设备初期调试阶段,故障率的确高于生命周期的平均故障率,但到了设备中期,故障率波动较为明显。同时,两种品牌的加工中心为了消除维修人员技能等方面的影响因素,根据两种品牌加工中心的故障次数进行了类似统计(由于加工中心数量较多,此故障次数为每小时设备平均故障次数),设备故障次数围绕故障率呈现一致的波动状态。由于加工中心结构复杂,牵涉到液压、气动、机械结构、电控等多方面因素,所以故障特征与传统设备完全不同,“浴盆曲线”原理已经难以适用于现代加工设备。经分析大致得知两点:一是加工中心在气温分别较高和较低的夏季和冬季,或者湿度较大的情况下,故障率较高;二是设备在长时间停机后开机,故障率较高,并且当设备是单班生产时,故障率要高于两班和三班生产模式。综上,传统设备维修管理理论对于类似于数控加工中心的先进制造设备已具有明显的局限性。如何在传统维修理论的基础上进行发展和创新,将是很多制造企业迫切需要解决的一大难题。
二、数控加工中心结构及故障特点
数控加工中心是集机、电、液压、气动为一体的设备,其核心就是数控技术。目前加工中心已基本使用计算机数控技术(CNC技术),一次装夹就能够实现加工出较复杂的零件,并且在加工余量大的情况下,能够实现高精度(0.001 mm)。由于数控加工中心的柔性化程度高,所以其故障也呈现出多元化的特点。以缸盖一线加工中心的故障历史数据为例,将该加工中心的部件系统分为以下11类:
(1)冷却系统:水泵、水管及附带的压力、流量、温度信号;
(2)润滑系统:集中润滑总成,包含润滑电机、油箱、密封、过滤器等;
(3)排屑系统:将机床内的铁屑或铝屑排出的系统,包括排屑链、排屑电机、挂屑器、排液泵等;
(4)电器系统:包含接触器、熔断器、继电器、按钮、连接线缆等装置,同时也包括逻辑可编程控制器(PLC)、输入输出装置(I/O)、屏幕(OP)、操作面板(MCP)等;
(5)伺服系统:用来精确地跟随或复现某个过程的反馈控制系统,包含伺服电机、编码器、变频器、中央控制单元、驱动控制模块等;
(6)主轴系统:主要指电主轴及相关附件;
(7)液压系统:包含动力元件、执行元件、控制元件、辅助元件(附件)和液压油五大部分,主要部件为液压泵、油缸、阀、油温油位计等;
(8)气动系统:通过以压缩空气为工作介质传递动力或信号的方式提供动力的系统;
(9)刀库系统:这里主要指盘式刀库及其相关附件;
(10)进给系统:X、Y、Z轴进给系统及相关部件,包括导轨、滑块、丝杆等;
(11)机械附件:包含夹具、联动板、防护板等机械部件。
根据上述分类,对2010年~2016年的历史故障数据进行了汇总和分析,如图1所示。其中故障平均维修时间为故障维修总时间除以故障次数。可以看出,按照平均维修时间排序,维修时间最长的四个系统依次为主轴系统、进给系统、刀库系统和排屑系统。目前,很多制造企业采用OEE(Overall Equipment Effectiveness)作为考核设备开工率的指标。OEE是一个独立的测量工具,它用来表现实际生产能力相对于计划产能的比率,其中设备故障及磨损是影响实际生产能力的重要因素。所以降低设备故障率和减少设备停机时间对于提升企业生产能力、尤其是针对平均维修时间较长的系统是极为重要的。
图1 各系统故障平均维修时间(2010年~2016年)
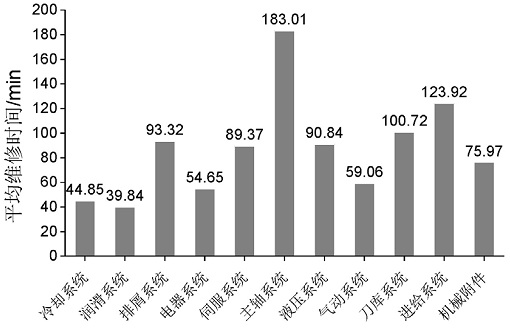
三、数控加工中心维修工具及方法
目前,设备抢修(应急维修)已远远不能满足现代企业的要求。随着科技的进步,维修理论也经历了由应急维修和定期性预防维修,到以可靠性为中心的维修(RCM)和基于状态的维修(CBM)的转变,维修方法及工具也逐渐丰富。以某发动机厂为例,除应急维修外,整个维修体系包含了日常设备巡检、设备专业点检、月度保养(TPM)、年度保养和重大及重复性故障分析等。
主轴系统故障、进给系统故障、刀库系统故障及排屑系统故障是该数控加工中心维修时间最长的四个部件,针对这些易造成重大故障的部件(本文定义维修时间超过240 min为重大故障),制定了设备专业点检体系,结合状态维修理念进行设备的预防性维护。
1、电主轴
电主轴是将变频电机与机床主轴合二为一的主轴,属于集成式的主轴单元,实现了机床的“零传动”,具有转速高、功率大的特点。本文例举的缸盖加工中心采用的是最高转速达24000r/min的电主轴,实现了高速和精密切削的要求。由于电主轴价值昂贵(达20余万元),更换时间长且过程复杂,所以对电主轴进行预防性维护十分必要。
电主轴的常见故障主要有轴承损伤、刀具夹爪损伤、拉刀夹紧力下降和一些电气故障(如线圈烧坏、传感器损坏等),针对上述故障,制定针对主轴的专业点检项目:
① 测量主轴径向跳动及不平衡量;
② 测量主轴放松时端面伸出量,对不符合要求的进行调整;
③ 测量主轴握刀夹紧力,对不符合要求的进行调整;
④ 检查HSK夹头磨损情况,对磨损夹头进行更换;
⑤ 高压切削液有无泄漏(管路和旋转接头);
⑥ 检查主轴夹头与刀柄密封圈有无磨损,视情况更换。
2、进给系统
本文例举的数控机床采用直线电机、导轨滑块和光栅尺作为进给系统的组成部分。对于上述部件构成的进给系统,同样面临着更换时间长、更换过程复杂的情况,并且由于数控机床伺服系统实现了对机械运动的实时监控,所以当进给系统报警时,现象往往不明显,报警内容的指向性不是很强,需要维修人员进行一系列分析后,方能确定具体的故障原因或损坏部件,所以诊断时间也较长。
分析该数控机床进给系统的历史维修数据,发现造成进给系统故障的主要原因为润滑不足(该加工中心采用手动加注油脂的润滑方式),所以预防性检查和维护十分必要。以下是针对该机床进给系统制定的专业点检项目:
① 检查导轨滑块润滑情况( 视情况加润滑脂);
② 检查滑动阻力是否过大;
③ 检查导轨滑块刮屑器是否正常;
④ 检查导轨定位面是否能塞进0.02 mm塞片;
⑤ 检查光栅尺气密0.4~0.7 bar,检查气管是否出气;
⑥ 检查光栅尺读头与尺身的间隙;
⑦ 检查缓冲器有无损坏(视情况更换);
⑧ 测量机床精度。
3、刀库系统
数控机床刀库系统的工作原理是由伺服电机配合减速箱对盘式刀库进行驱动,该刀库具有响应速度快的特点,但是频繁的抓放刀过程也容易造成刀库卡爪及刀盘变形。针对上述问题,需要对刀库进行定期检查,避免刀库故障造成的生产损失。以下是针对刀库系统的专业点检项目:
① 检查刀盘是否有晃动,减速箱工作是否正常;
② 检查刀爪、弹簧和刀具限位机构;
③ 检查主轴在刀库上的抓放刀位置是否准确。
4、排屑系统
排屑系统是用于对加工过程中产生的铝屑进行清理,避免铝屑在机床内部堆积;由于排屑链的链条较长,一旦发生排屑链堵转或者排屑链断裂,维修时间将大幅度增加。为了避免类似情况的发生,定期检查排屑链的松紧及磨损情况就十分必要。
在确定对关键部件的检查项目后,就要对检查周期进行合理安排。合理的检查周期不仅能够实现将故障消灭在萌芽状态,以降低故障率,而且可以避免预防性维修频次过高造成的人力及材料费用的浪费。
按照供应商提供的资料,机床进给系统、刀库及排屑系统的建议保养周期为一年一次,电主轴的保养项目中更换主轴密封件的要求频次最高,为一季度一次(以上周期都是在每天8小时工作制基础上制定的)。结合生产中实际的历史故障频次及数据(如表1所示),决定将检查周期进行一定调整。
表1 2010年~2013年单台故障次数累计
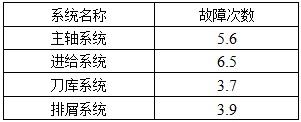
从表1可以计算出,主轴系统、进给系统、刀库系统及排屑系统平均每年单台故障次数分别为1.4次、1.6次、0.92次、0.97次,综合供应商提供的数据,决定将以上四大系统的专业点检周期设定为一季度一次、半年一次、一年一次、一年一次。通过日常巡检、月度保养(TPM)、年度保养结合设备专业点检的预防性保养体系,降低了加工中心的故障率,四大系统的平均每年单台故障次数下降至0.75次、0.65次、0.47次、0.49次,提升了设备开工率。
四、基于状态的维修(CBM)在加工中心的应用
基于状态的维修(CBM)是一种全新的设备维护方式,主张基于设备状态检测信息采取相应维护措施。它的产生是基于传感器技术、信号处理技术、计算机技术的发展,核心思想是在有证据表明故障将要发生时才对设备进行维护,目的是准确地检测和判断设备运行中所处状态以及环境条件,利用这些信息对设备预期的可使用寿命进行预测,有针对性地制定设备维护计划。
目前,国内外较为典型的状态监测方式主要有离线定期监测、在线监测离线分析的监测、在线监测。对于旋转类运动设备,主要有以下四个方面的监测诊断工作:
1、振动监测
振动可以敏锐地发现回转或往复机械异常指标和故障,通过对振动信号的采样和数据处理,就可以把握机器的劣化程度和异常现象,使机器和零部件的寿命得以最大限度使用,并且分清故障性质,方便地决定维修时间和范围,延长了检修周期,确保机器正常运行。振动诊断主要有简易诊断和精密诊断两种模式。作为设备诊断技术中最先进的技术,振动监测已在生产现场广为应用,是目前最常用的诊断手段,主要用于对运转设备的水平、垂直、轴向振动进行定量测量,及时发现潜在故障。目前对取得的振动信号的分析方法有“频谱”、“倒频谱”、“振动加速度包络”等。振动测量是最有效判断运转设备状态的方法之一。
2、温度监测
在工业生产中,“温度”这一参数约占测量总量的50%左右。因此,设备或生产过程的温度(或称热状态)监测是设备诊断技术的一个重要部分。利用温度监测,可以迅速准确找出设备的过热故障点,提供机械设备预知维修的有关信息,并在产品检验、结构改进、节能降耗等方面发挥显著作用,是开展设备诊断工作的一个重点项目。随着现代科学技术的发展,红外测温仪器大量应用于温度监测诊断设备故障领域中。红外测温技术是温度监测工作的一个专门技术领域,它在生产实践中不断发展而日趋完善,逐渐渗透到工业各部门中。这种技术在许多领域内已经成为不可替代的工具,正在由一种现代化的测温技术转变为一种较为全面的设备状态监测和故障诊断的实用方法。
3、电流(功率)监测
电流或功率监测对电机起到运行监护的作用,在生产中广为运用,是保护电机的重要手段,也是对电机进行远程控制的重要远传参数之一。主要仪表为电流表、功率表、电压表等。
4、压力监测
在化工生产中,整个系统的压力是非常重要的。反应和输送过程中压力控制的好坏不仅涉及经济性,更重要的是安全问题。它也是国家在设计规范和安全附属设施中要求定期检测的项目。主要仪表有现场仪表和远传仪表。
随着数控加工中心朝着自动化和智能化的方向发展,机床自带的在线监测设备也越来越多,为了丰富设备状态监测的工具和方法,专业的离线状态监测工具正逐步在加工中心现场进行应用。以本文提到的加工中心为例,测力计、振动分析仪、示波器、球杆仪、编码器检测仪、Profibus网络诊断器及便携式动平衡机等已经开始投入使用,如表2所示。
表2 监测工具的使用
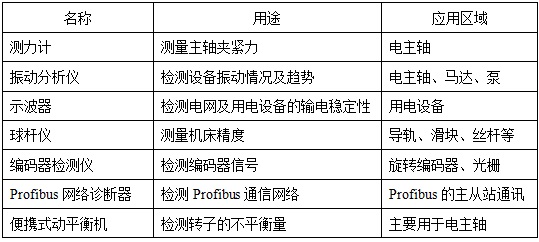
结合状态监测工具,在关键部件的专业点检过程中实现了精确化诊断和状态趋势预测,发现了很多常规手段难以察觉的故障隐患,对设备的预防性维护实现了助力和提升,并对备件的预防性更换周期和设备专业点检周期进行了优化和微调,在降低设备故障率的同时,也减少了设备维护材料使用量和人工成本,尤其是在对电主轴、导轨滑块、丝杆、泵等关键部件的预防性维护上效果显著。
五、结语
目前大多数企业采用机械化的定期设备保养的方法,相比传统的以抢修为主的维修思路有了很大提升,但是仍存在“设备维护不足”和“设备维护过剩”的风险,造成设备、产量损失和成本浪费。
基于状态的维修理念正逐步发展,该方法通过状态监测及状态诊断等判断设备的劣化程度。本文将基于状态的维修理念与设备专业点检机制相结合,通过状态监测及诊断优化设备专业点检项目、方法及点检周期。在生产应用中,该维修策略起到了降低设备故障率和提升设备开工率(OEE)的效果。实践表明:设备开工率达到90%左右,验证了该维修策略的有效性。
作者:高衡 单位:上海交通大学机械与动力工程学院